2016.2.18
Industry4.0現場からの進め方【山田太郎の生き残りのためのスペックマネジメント術 vol4】
山田太郎の生き残りのためのスペックマネジメント術 vol.4
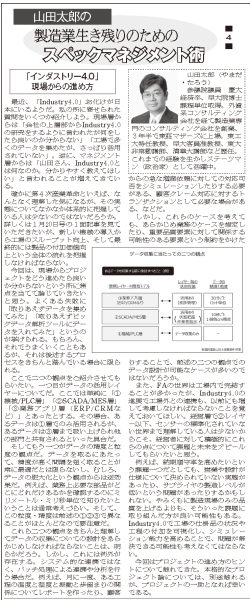
最近、「Industry4.0」お化けが日本にいるようだ。私の所に寄せられた質問をいくつか紹介しよう。現場層からは「会社の上層部からIndustry4.0の研究をするように言われたが何をしたら良いのか分からない」「工場で多くのデータを集めたが、さっぱり活用されていない」逆に、マネジメント層からは「山田さん、Industry4.0とは何なのか。分かりやすく教えて欲しい」と言われることが増えてきている。
確かに第四次産業革命といえば、なんとなく理解した気になるが、その実態についてなかなか体系的に把握している人は少ないのではないだろうか。詳しくは1月20日号の1面記事を見て頂きたいが、新しい機械の導入から工場のスループット向上、そして最終的には製品の付加価値向上という全体の流れを把握しなければならない。
今回は、現場からプロジェクトをどう進めたら良いか分からないという所に焦点を当てて論じていきたいと思う。よくある失敗に「とりあえずデータを集めてみた」「とりあえずビックデータ解析ツールにデータを入れてみた」というのが上げられる。もちろん、それで上手くいくこともあるが、それは後述するプロセスをきちんと踏んでいる場合に限られる。
ここで2つの観点をご紹介させてもらいたい。1つ目がデータの活用レイヤーについてだ。ここでは単純に「①機械/PLC層」「②SCADA/MES層」「③業務アプリ層(ERP/CRMなど)」とあったとする。その場合、あるデータは①層でのみ活用されるが、あるデータは③層まで吸い上げられ他の部門と共有されるといった具合だ。
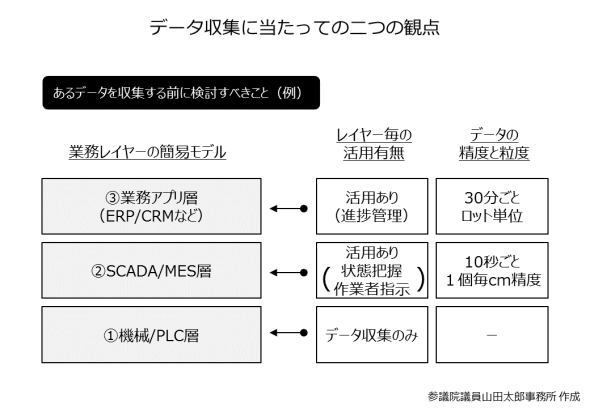
そしてもう一つがデータの精度と粒度の観点だ。データをとるにあたって、精度高く、間隔を短く取ることが常に最適だとは限らないし、むしろ、データの肥大化という観点からは逆効果だ。例えば、業務上必要な部品がどこにどれだけあるかを確認するのにミリメートル・ミリ秒単位で知りたいということは通常考えづらい。そして、この粒度・精度は前述の①②③で異なることがほとんどなので要注意だ。
これら二つの観点をきちんと理解してデータの収集についての設計を予めしなければならないことは、明らかだろう。しかし、これには例外が存在する。システム的な連携ではなく、バッチ処理による連携や分析を行う場合だ。例えば、月に一度、ある工程の温度と湿度と振動と歩留まりの関係についてレポートを作ったり、顧客からの急な増産依頼に対しての対応可否をシミュレーションする必要がある、顧客クレーム対応に対するトランザクションとして必要な場合があるなどだ。
しかし、これらのケースを考えても、予め業務のケースを想定したり、重要品質要素に対して関係する可能性のある要素という制約をかけることで、前述の2つの観点でのデータ設計が可能なケースが多いのではないだろうか。
また、FAの世界は工場内で完結することが多かったが、Industry4.0の進展で工場外との連携も、以前にも増して考慮しなければならないことを覚えておいて欲しい。経営層で②レイヤー以下、センサーの標準化されていない世界まで理解している人は少ないからこそ、経営者に対して積極的にこれらの点について課題と未来をアピールいってもらいたいと思う。
例えば、納期遵守率を高めたいという課題一つだとしても、営業や設計が仕様について決められていない実態があったり、サプライヤの製造レベルが低いという問題もあるかもしれない。闇雲に製造現場のみの品質を上げるよりも、そういった課題に取り組んだ方が良い可能性もある。Industry4.0で工場の仕掛品の状況や工程の付加を可視化し、シミュレーション能力を高めることで、問題が解決できる可能性も考えなくてはならない。
今回はプロジェクトの進め方のヒントについて触れてきた。本格的なプロジェクト論については、別途触れるが、プロジェクトの一助となれば幸いである。
(オートメーション新聞 2016年1月20日号)