2016.1.26
Industry4.0が提示する解決策【第76回山田太郎ボイス】
山田太郎の製造業は高度な情報産業だ!vol.5
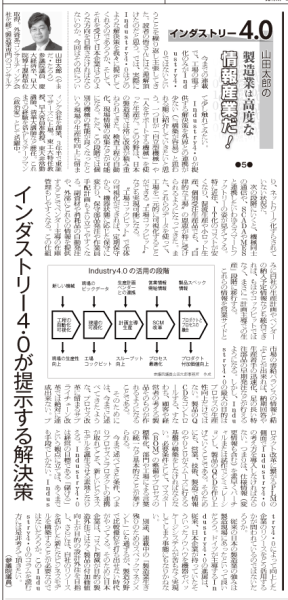
今までの連載で、工場の電子化のみがIndustry4.0ではないということを繰り返し主張してきた。読者の皆さんにはご理解頂けたのだと思う。では、実際にIndustry4.0はどのような解決策を我々に提示してくれるのであろうか、そして、それを受けて日本企業はどのような方向を目指さなければならないのか。今日はその点について少し触れてみたい。
Industry4.0が提供する解決策を外界との連携が少ない(≒構築が容易)と思われる順に紹介していきたいと思う。一つ目が「自立型機械」や「人をサポートする機械」を使った生産だ。この分野は、日本の製造業では常に改善が積み重ねられてきた。検査工程の自動化、現場情報の収集などが可能になる。ただ、この段階では個別の機械の性能が良くなったという現場の生産性向上に留まり、ネットワーク化すらされていない状況だ。
次の段階にいくと、機械同士の通信や、SCADAやMESと連携したいわゆるスマートファクトリーの姿が見えてくる。特に近年、IT化のコストが安くなり、混流生産や小ロット生産、個別受注生産品でも、“自律的な工場”の恩恵が特に受けられるようになってきた。また、これらのデータを使って、工場を一元的に可視化することができる“工場コックピット”なども実現可能になる。
“工場コックピット”で全体の可視化ができれば、定期保守から、機器状態に応じた保守に変わり、保守部品発注や作業員手配計画もより立てやすくなる。副資材や消耗品の自動発注や、外部にこれらの情報を提供することでベンダー主導の在庫管理もしやすくなる。この仕組みに自社の生産計画やベンダーの納入予定情報なども統合できれば、もはやコックピットではなく、まさに「計画主導での生産」段階に移行する。
これらの情報を営業サイドと市場の需給バランスの情報と結ぶことが出来れば、納期回答や生産着手の迅速化、足の長い特注部品の早期発注などが行えるようになる。しかし、Industry4.0の最大の目的はプロセスの生産性向上だけではない。製品のQCDをコントロールする、すなわち、顧客や経営者の考える製品そのものが作れるようになることである。
そのためには、今までに述べてきたような、プロセス改革に留まるサプライチェーン改革では絶対に達成出来ない。プロダクト改革に繋がるPLMの側面でIndustry4.0の考え方を導入しなければならない。つまりは、仕様情報(変更情報も含む)を素早くバーチャルまたは試作でシミュレーションし、製品のQCDを作り上げていくことである。そのためにも、営業、技術、製造で情報のやりとりがスムーズに行える基盤の構築をしなければならない。必要条件として、マスター(BOM)の整備やプロセスの標準化、部門や工場による言葉の統一など基本的なことが上げられる。
今まで述べてきた条件、つまりプロセスとプロダクトの連携が取れてこそ、新しいビジネスモデルが誕生させる素地となりえる。Industry4.0は経営の目標である「儲ける」という観点に立てば、あくまでも手段でしかない。Industry4.0によって向上した企業のリソースをどう活用するかが問われているのではないだろうか。
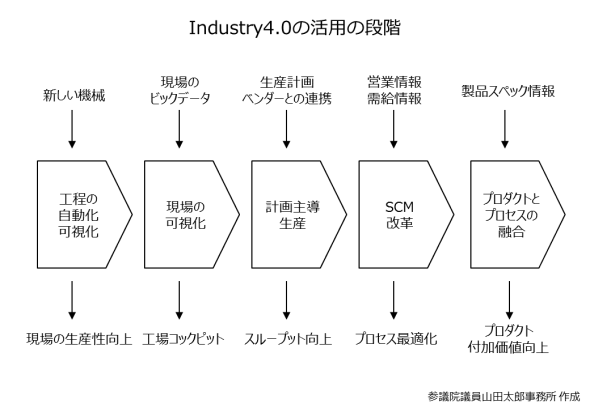
従来の日本の製造業の強みは製造現場にあったといって良いだろう。ドイツが主導するIndustry4.0の進展は、従来、日本企業が持っていたそういったノウハウを機器やパッケージシステムが苦も無く実現してしまう事態にもなりかねない。
別途、連載中の「製造業生き残りのためのスペックマネジメント」にも通ずるが、製造分野で比較優位を打ち出せない時代がやってくる。そのために日本企業は、コスト削減が目的の製造外注ではなく製品の付加価値向上が目的の設計外注を目指し、さらには、自社のリソースを活かした新たなビジネスモデルを構築することが必要なのではないだろうか。このIndustry4.0のコラムを読む方には是非考えて頂きたい。
(オートメーション新聞 2016年1月20日号)